|
|
|
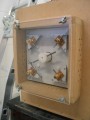 |
|
The DC coil needs a high breakrate spark gap, or the
gap may power-arc and stop the coil from working very
well. The breakrate doesn't need to be a multiple of
line-frequency (50Hz in my case) because, well, it's
running on DC. There is no line frequency. So the motor
driving the spark gap doesn't need any modification, just
a cheap universal motor will do. I've gone with a
propellor gap design - the rotor is light and doesn't
require much in the way of torque to spin. So I've used
most of a mini palm-sander, which is supposed to run at
10,000rpm. The box says 135W, so the motor's pretty
small. It does sound like it's about to explode when run
full-out unloaded, so I'll control the input to it with a
2.5A variac I happen to have lurking somewhere.
|
|
|
|
|
|
|
|
|
|
|
|
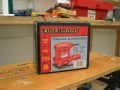 |
|
The palm sander wasn't very expensive anyway, so I
didn't feel too bad about taking it apart. In fact I
probably felt better taking it apart than I would've done
using it for its genuinely real intended purpose. I'm not
convinced about the wisdom of attempting to use $20 power
tools for anything sensible, it seems like asking for
trouble. I mean, I can damage myself with expensive
properly-made ones just fine, thanks. |
|
|
|
|
|
|
|
|
|
|
|
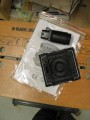 |
|
So, once you've got your mini palm-sander, carefully
remove these bits. And throw them away. Also ensure you
discard the instruction booklet, it won't be any use
where we're going. There was also an eccentric
drive-thingy and bearing on the end of the motor shaft,
that fitted into the hole in the sanding foot. But I
filed it off and forgot to take a photo so I can't show
you what it looked like.
|
|
|
|
|
|
|
|
|
|
|
|
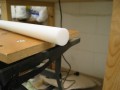 |
|
This is the plastic rod I made the rotor hub from.
It's 30mm diameter, and fairly tough. I imagine letting
it get hot might lead to all sorts of unfortunate
occurences, since it could soften and not hold the motor
shaft and propellor electrode as firmly as it should. I
found it difficult to get the accuracy I really wanted
making the hub, and it's still not spinning quite true.
I've left the spacing between the propellor and the
static electrodes quite wide to make sure that if the hub
wobbles the electrodes won't crash into each other. At
some stage I'll have another go at it (I might be able to
borrow a lathe, which would help a lot) - a more stable
hub seems likely to last longer, be generally safer and
will let me make the gaps narrower, so hopefully they
won't be as lossy.
|
|
|
|
|
|
|
|
|
|
|
|
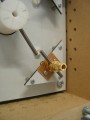 |
|
The electrodes (four static and one propellor) are
made from tungsten rod for arc welding. I got the plain
kind - I was slightly concerned about cutting/grinding
thoriated tungsten rod since presumably little chunks of
thoriated tungsten ping off and irradiate stuff as
you're doing it. The static electrodes are clamped into
little screw-terminals that I think are meant for
speaker-wire connections.
|
|